The Role of CNC Machines in Industrial Applications
- JC
- Mar 31
- 4 min read
CNC (Computer Numerical Control) machines have revolutionized industrial manufacturing, providing precision and efficiency in production processes. These machines, which can automate various tasks such as cutting, milling, and drilling, have been adopted widely across different sectors. In this blog post, we will dive deeper into the role of CNC machines in industrial applications, exploring their benefits, types, and real-world applications.
CNC Machines: An Overview
CNC machines consist of a computer control system that dictates the movement of machinery and tools. This level of automation ensures high accuracy and productivity. CNC machines are invaluable in industries such as aerospace, automotive, and manufacturing, as they can produce intricate components at a pace and precision level unmatched by manual processes.
Over the past few decades, CNC technology has evolved significantly. Modern CNC machines not only enhance productivity but also allow for the production of complex geometries that would be difficult or impossible to achieve using traditional machining techniques. For example, CNC milling machines can create parts with twisting geometries, while CNC lathes can manufacture symmetrical objects with precision.
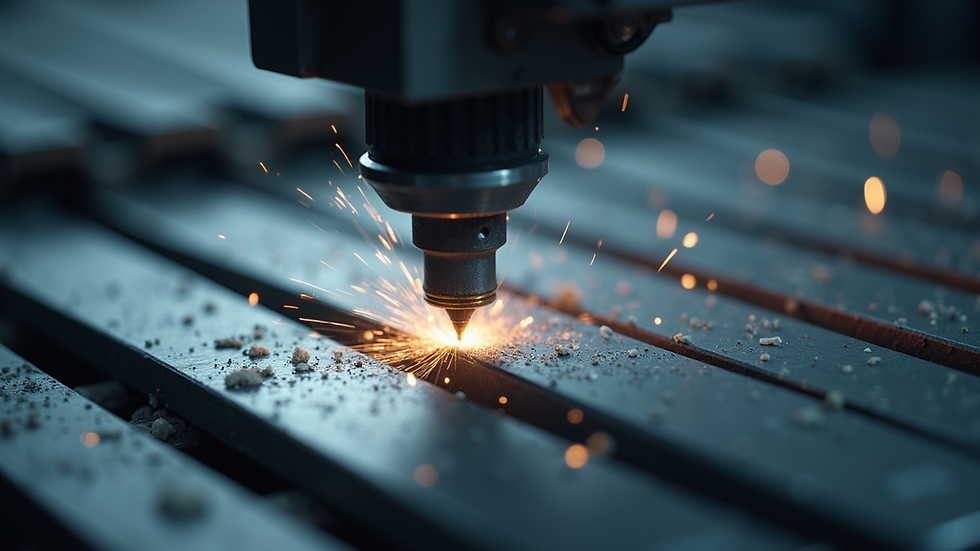
The Advantages of Using CNC Machines
CNC machines come with numerous advantages that contribute to their widespread adoption in the industrial sector. Here are some key benefits:
Improved Precision and Consistency: CNC machines can produce parts with high precision and repeatability. Once a design is input into the computer, the machine can replicate it multiple times without sacrificing quality. This consistency is crucial for industries where tolerance levels are confined and even a slight deviation can result in defective products.
Increased Efficiency: Automation leads to faster production rates. CNC machines can operate round the clock with minimal supervision, which greatly enhances throughput. According to a study by the National Association of Manufacturers, companies that utilize CNC technology have seen productivity increases of 20-30%.
Enhanced Safety: CNC machines reduce the risk of accidents that can occur with manual machining. Operators can work from a safe distance while the machine performs the tasks. This feature minimizes workplace injuries, resulting in a safer work environment.
Flexibility in Production: CNC machines can be easily adjusted to produce different parts using the same equipment. This flexibility is particularly beneficial for manufacturers catering to diverse clients with various specifications.
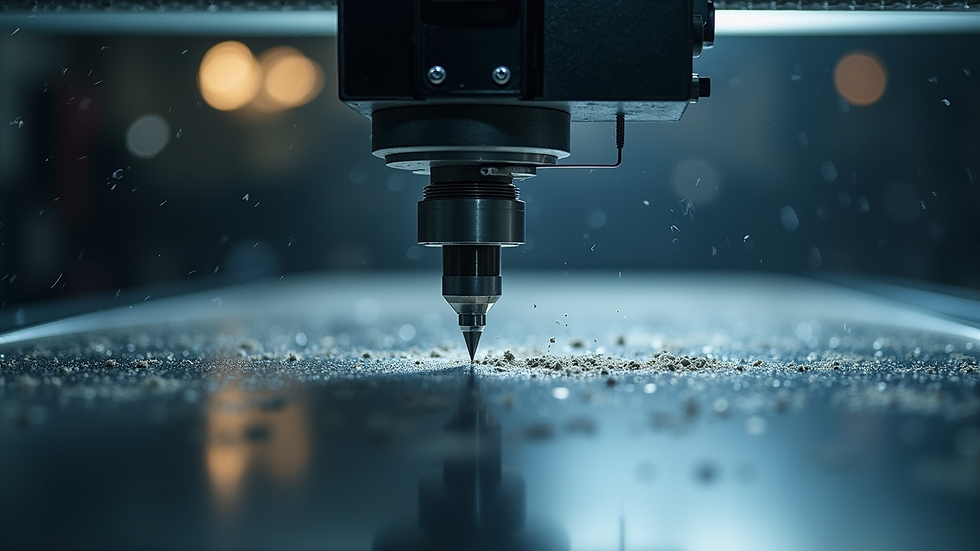
What Does Industrial Machinery Do?
Industrial machinery encompasses various devices and equipment used in the manufacturing process. These machines perform specific functions, ensuring the efficiency and reliability of production. They can be broadly categorized into two segments:
Production Machinery: This includes CNC machines, mills, lathes, and injection molding machines. They are primarily focused on creating parts, products, and materials in bulk.
Material Handling Machinery: Equipment such as conveyors, forklifts, and hoists that transport materials from one point to another fall under this category. They ensure that raw materials and finished products move seamlessly through the production cycle.
CNC machines are particularly important in production machinery. Their ability to work with a variety of materials such as metal, plastic, and wood makes them versatile. This versatility allows for broad applications across different industries.

Common Applications of CNC Machines
CNC machines find applications in numerous fields. Here are some common uses:
Aerospace Industry: The aerospace field requires components that meet strict safety standards and tolerances. CNC machines can produce complex geometries for aircraft frames, turbine components, and engine parts with exceptional precision.
Automotive Manufacturing: Car manufacturers utilize CNC machines to create engine blocks, transmission housings, and other critical components. CNC technology enables them to produce lightweight parts that conform to fuel efficiency and performance standards.
Medical Device Production: CNC machines are vital in producing tools, implants, and other medical devices. The medical industry demands high-quality production standards, making CNC technology indispensable.
Electronics: Printed circuit boards (PCBs) and casings for electronic devices are often manufactured using CNC machines. These machines can create intricate designs that fit within the compact spaces of electronic products.
Furniture and Carpentry: In the furniture industry, CNC routers can cut and shape wood and composite materials. This allows for creating customized designs, enhancing aesthetics while maintaining functionality.
The Future of CNC Machines
The future of CNC machines is promising, with several trends shaping the industry.
Integration of AI and Machine Learning: The advent of artificial intelligence can further enhance the efficiency of CNC machines. AI can monitor processes, predict maintenance needs, and optimize machining paths, resulting in improved productivity and reduced downtime.
3D Printing Convergence: The melding of CNC machining with 3D printing technologies offers exciting opportunities for manufacturing. This combination can allow for more complex designs and faster prototyping.
Sustainability Efforts: As industries aim for greener practices, CNC machines can contribute significantly. Their efficiency reduces material waste and energy consumption, promoting a more sustainable manufacturing process.
Remote Monitoring: With the rise of IoT (Internet of Things), manufacturers can implement remote monitoring systems for their CNC machines. This development enables real-time tracking of performance and maintenance needs, enhancing operational efficiency.
A Key Player in Industrial Solutions
Understanding the expansive capabilities of CNC technology is critical for businesses seeking to enhance their manufacturing processes. By integrating CNC machines into your operations, you can leverage industrial machine solutions to improve output, quality, and safety. The future of CNC machines holds potential that companies should embrace to keep up with the evolving demands of the industry.
In summary, CNC machines are integral to modern manufacturing, providing unmatched precision, efficiency, and safety. As technology continues to advance, exploring the potential applications and benefits of CNC machines will be vital for successful industrial operations. Whether in aerospace, automotive, or any other sector, the role of CNC machines cannot be overstated.
Comments